多軸滑塊式熱室壓鑄機
“傳統(tǒng)的”熱室壓鑄機一般都有兩塊車壁,一塊移動和一塊固定。各半邊的模具藉由使用各種機械裝置(例如:壓板)固定在各自的車壁上。各種復雜的零組件都可建置在模具內來壓鑄生產。然而,由于運動部件的磨損,重現(xiàn)精度(零件的一致性)會受到隨著時間推移的影響,而模具是昂貴的。在每一次射出動作產生時,液態(tài)金屬經(jīng)由固定車壁上的模具澆鑄口和流道系統(tǒng)填入模腔內。壓鑄件通常需要做澆口和流道的金屬廢料之修剪加工操作。為了避免射料時空氣從澆口混入鑄件,常見的做法是在模具上添加溢料口和排氣溝。溢料口會進一步增加廢料,而排氣溝也往往會造成模腔周圍產生毛邊。
“多滑塊”熱室壓鑄機具有兩個或兩個以上的獨立可移動滑塊。每個滑塊搭載著一個模塊在一套精密滑動導向系統(tǒng)內進行操作(也被稱為十字滑座)。使用高達四個滑塊是常見的,六個滑塊也是可能的。在每個模塊面上有一個或多個模腔和/或抽芯,共同形成完整的型腔和流道輪廓(在將熔融金屬注入后)。各模塊的配合面被一套鎖模系統(tǒng)結合在一起,然后熔融金屬由垂直于模塊配合面的方向射入(“分型面注射”)。 因為直接射料在分模面,所以沒有澆鑄口。因此,減少廢料,并且周期時間往往要快得多,因為開模前并不需要等待澆鑄口固化。并且,要在傳統(tǒng)的壓鑄機鑄造復雜零件的各種機械裝置之需求,在多滑塊機上通過使用一個額外的滑塊就可以免除。零件的一致性提高和模具成本降低。沒有澆鑄口和顯著降低溢流口的需求(通常,是沒有必要的),以及排氣的要求是最小的,從而節(jié)省材料。
多滑塊模具是使用設計成4個垂直方向的滑塊模具,能夠用來生產很復雜且精密的鑄件。有時候,模具被設計成90度以外的角度就可使用多達6個滑塊。此制程主要被使用于細小的鋅鑄品。
多滑塊模具是由模塊 (Die Block)、滑塊 (Slide)、十字滑座 (Cross Head)和蓋板 (Cover Plate)所組成。每一個模塊在它的模面上有各自的型腔或型芯 (Cores),合在一起形成完整的型腔和供給熔融金屬注入的澆道。這些模塊被安裝到滑塊上,準確地配合進十字模座內,確保能重復啟閉的操作。在模具的頂面栓上一塊蓋板,把所有這些模具組件結合在一起。
每一個滑塊都受控于控制器,且在關閉和打開的順序期間都能各自獨立地移動。如此提供了極大的靈活性,以確保零件的完整和防止對模具的損害。
在模具開啟后使用強氣流將整個型腔射出物 (鑄件) 吹進一個裝有填料墊的收集裝置,達成鑄件的押出。
多滑塊和分模面射出的壓鑄技術用于生產小型零組件具有以下眾所皆知的特性:
- 高精度;
- 可壓鑄具有復雜幾何形狀的精密零件;
- 零件的質量一致;
- 換模速度快;
- 可做模內自動斷澆;
- 鑄件無毛邊;
- 循環(huán)速度快;
- 模具成本低;
- 可免除或降低二次加工;
- 節(jié)省材料、能源及人工。
以上特性可證明一般使用多滑塊技術生產小型鑄件其結果是成本單價是最低的。
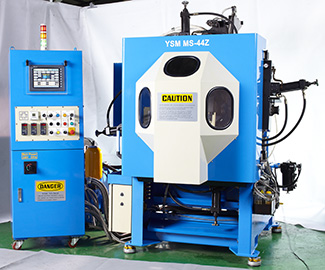 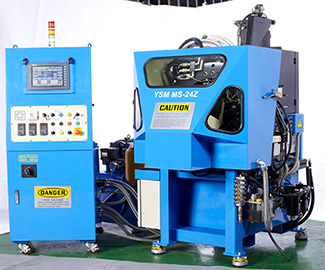
引言
多年以前,人們普遍認為多滑機不適合生產需要電鍍質量的鑄件,或是對于生產小型鑄件的電鍍質量并不是最好的。除了是很小的鑄件之外,一般小型壓鑄機并不具有生產非常高表面光潔度的質量所需要的射出功率。事實上,在當時有許多領先使用多滑塊機的業(yè)者采用生產較大鑄件的傳統(tǒng)壓鑄機完成那些電鍍質量表面光潔度需求的小鑄件。
有鑒于此,友勝在過去的幾年中,針對提高滑塊壓鑄機的射出功率、鎖模能力、多滑塊制程功能以及多滑塊模具設計等技術進行大量的研究,以滿足生產電鍍質量高表面光潔度鑄件的需求,結果總結如下。
鎖模系統(tǒng)
多年來,“C型”鎖模系統(tǒng)已被廣泛用于多滑塊壓鑄機,但鎖模力較低。這樣的系統(tǒng)是由小型氣動或液壓缸驅動,價格相對低廉,操作迅速,但只適于一般的輕型應用。然而,當壓鑄較大的部件,在注射壓力要達到高的表面光潔度和速度時,C型鎖模系統(tǒng)要保持緊閉則是一個挑戰(zhàn)。當今,C型鎖模系統(tǒng)已被適于重型應用的環(huán)式鎖模系統(tǒng)取代。
友勝MS系列滑塊機的環(huán)式鎖模系統(tǒng)以及滑塊導引系統(tǒng),是專為高表面光潔度鑄件的壓鑄應用所設計的。由四個大塊曲肘架支撐的曲肘機構以插銷錨入栓在桌板(車壁)上,有一個強力環(huán)栓在曲肘架的頂面。此組合得到非常剛性的效果 –環(huán)式系統(tǒng)基本上消除了桌板(車壁)的彎曲問題以及一般使用C型鎖模系統(tǒng)的曲肘架彈性變形特性。事實上,環(huán)式系統(tǒng)負載下的偏轉已被證明在相同噸位下小于C型鎖模系統(tǒng)的百分之10。
自動潤滑系統(tǒng)供應十字滑座和曲肘機構的所有組件的潤滑,從而大幅度地減少操作員介入的需要,并減少維護費用。
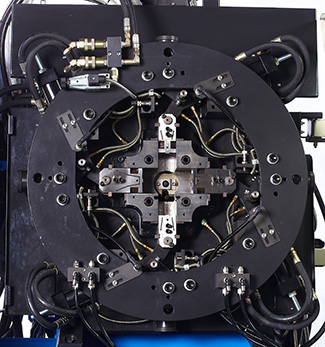 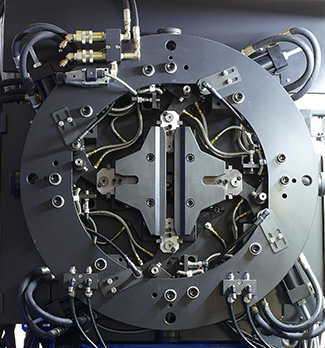
滑塊導引裝置
滑塊導引裝置(十字滑座)是完全獨立于鎖模系統(tǒng),并裝有可更換的耐磨板。裝載滑塊導引裝置的桌板 (車壁) 設有水冷卻回路,滑塊也一樣有。滑塊是由萬向榫接頭連接到鎖模系統(tǒng),拆裝方便快速,且滑塊無側向應力。各曲肘系統(tǒng)在其所屬的曲肘架中設有支撐滑塊曲桿的??繅K。此系統(tǒng)容許施加最大的預負載而十字滑座不會承載任何的推力。使用這樣的環(huán)形鎖模系統(tǒng),可以采用極高的射出速度和金屬壓力,模具不會“彈開”。
這樣的鎖模和滑塊導引系統(tǒng)的開發(fā)是多滑塊機實現(xiàn)高表面光潔度鑄件的最關鍵要素。
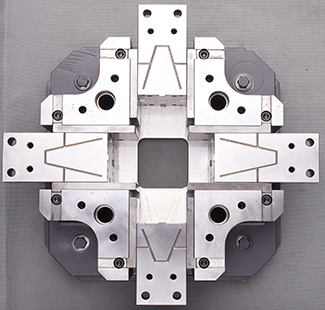
制程參數(shù)控制系統(tǒng)
所有的MS系列壓鑄機都配有一套可程序控制系統(tǒng),以及一個觸控人機界面,以便于編程、機器調試、程序存儲和檢索、集成存取控制,和一個錯誤訊息的聯(lián)機“求助” 系統(tǒng)。友勝專屬的最新一代控制系統(tǒng)軟件,不僅操作簡單,且功能強大的圖形界面降低了相關的“學習門坎”,非專業(yè)人員只需短期訓練即可正常操作新設備。乙太網(wǎng)絡模塊為選購配備,任何機器上的操作問題可通過它進行遠程診斷。
友勝開發(fā)的工藝參數(shù)和射出監(jiān)控系統(tǒng)(PPMS),為MS系列機種的選購項目。PPMS允許機器操作員設置多達12個關鍵生產參數(shù)的特定值(例如溫度、注射速度、和時間)。每個制程參數(shù)可以設定上限和下限。在一個設定條件范圍下進行檢測,PPMS可編程做如報警、停機等動作或直接將產品單獨分離,以做后續(xù)的檢驗。PPMS的射出監(jiān)控部分對于機器操作員和工藝工程師是一個很好的診斷工具。
閉回路射控制系統(tǒng)為MS-44機器的選購項目,可提供機器更大的可靠性和可重現(xiàn)性。此系統(tǒng)可從注射開始至完成的過程中實時控制,使系統(tǒng)性能穩(wěn)定,鑄件質量優(yōu),在注射結束時的“錘擊效應”顯著降低,從而減少毛邊。閉回路控制系統(tǒng)對于任何給定模具的所有設定,可以與模具動作順序和PPMS的設置一起被保存在電腦的硬盤上,方便重復性設置。
就超高速鑄造極小且精密的鑄件而言,型號MS-24是最理想的機種。
射出系統(tǒng)
整個射出系統(tǒng)是專為高性能和重現(xiàn)性所設計的,具有最大成型能力的效果。獨特的雙柱塞射出裝置,消除了鵝頸的射料通道之金屬液體回流,從而大大地減少注入模腔的空氣量,減少鑄件孔隙。
所有的MS系列機器都配有使用耐熱鋼精密加工做成的鵝頸,射出性能穩(wěn)定且使用壽命長久。
鵝頸管出口與噴嘴采用自動溫控電熱管加熱之設計。

金屬熔解系統(tǒng)
金屬熔解系統(tǒng)包含給料機、熔鍋和保護罩。為了能精確的控制料溫,采用電熱式熔鍋。位于熔鍋上方的給料機可預熱及自動填補料錠,并且保持熔鍋的熔湯料位一致和穩(wěn)定的溫度。熔爐圍繞保護罩確保人員安全并隔離發(fā)熱源,造就了干凈舒爽的工作環(huán)境。

油壓系統(tǒng)
完全集成式的液壓系統(tǒng)采用大流量、快速響應閥促使循環(huán)速度快速。鎖模功能的集成油路,同時控制了滑塊和鵝頸的動作。此油路板配備六個液壓功能,可供抽芯以及結合兩組氣動功能便于自動化的使用。獨立的射出油路板控制射出速度和壓力,從而導致一致的鑄件質量。
獨立式的液壓動力單元易于液壓泵和電機的調整和維修。液壓動力單元配備監(jiān)測液位和油溫以及過濾器狀況的傳感器。這些傳感器與控制軟件連接,發(fā)生任何異常情況時將產生報警信息通知操作者。
|